Methane Pyrolysis in Molten Metallic Catalysts
VIDEO
coming soon...
Introduction
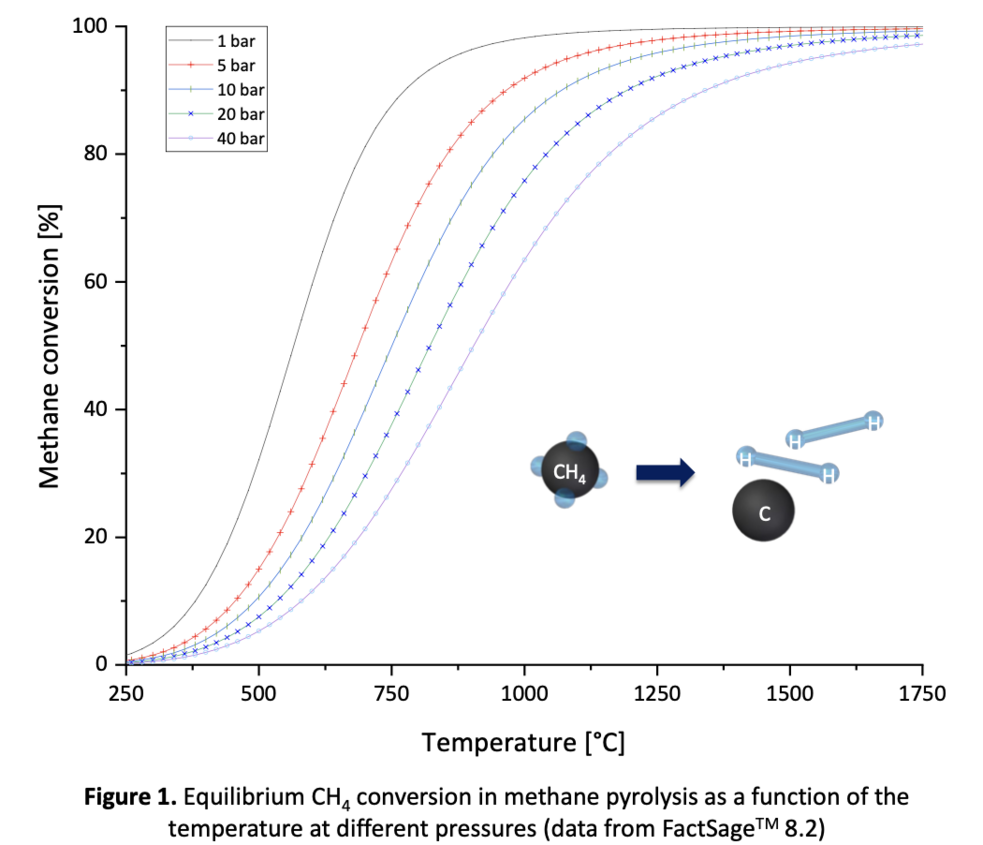
To cover the enormous growth in hydrogen demand predicted over the following decades, focus on research into clean technical solutions for H2 production is crucial. Methane pyrolysis represents a promising possibility to generate hydrogen and solid carbon with minimal CO2 emissions and is significantly less endothermic than water electrolysis. [1]
According to a thermodynamic equilibrium calculation of the methane pyrolysis reaction, 96 % of CH4 is decomposed at 900 °C and 1 bar (cf. Figure 1). However, achieving a reasonable reaction rate at these process conditions is difficult due to kinetic limitations. Catalysts can enhance the reaction rate and overall process efficiency. [2]
Various solid catalysts have been studied, including carbonaceous materials and transition metals. Unfortunately, these catalysts lose effectiveness at high temperatures due to coking. Utilizing molten metals and alloys as catalysts can mitigate deactivation, as the pyrolysis carbon floats on the liquid catalyst due to density differences. Furthermore, this effect facilitates an industrially feasible process to remove the solid product. [2]
Method
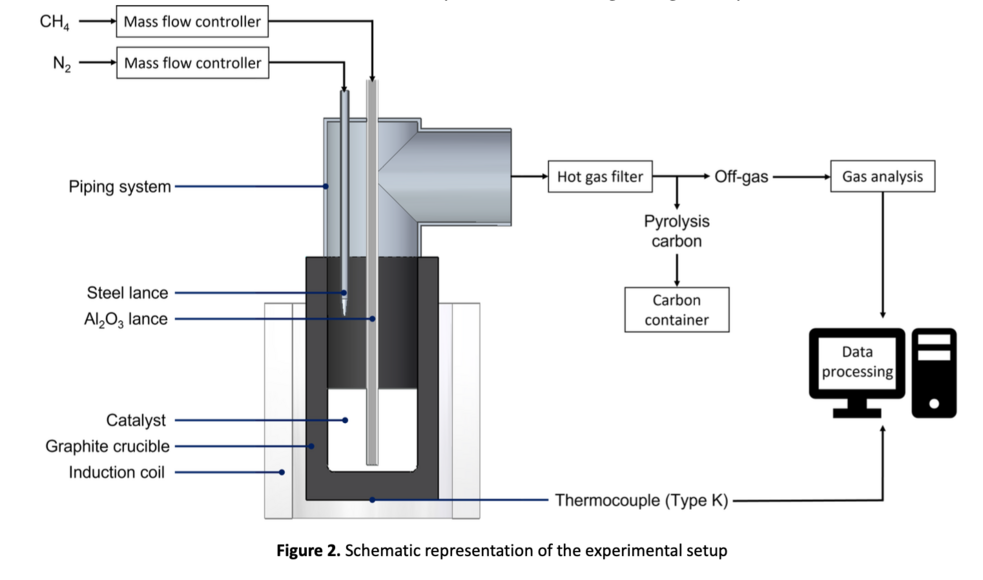
A schematic representation of the experimental setup is depicted in Figure 2. The reaction vessel containing the liquid metallic catalyst is connected to a piping system to generate a hermetically sealed system. An induction coil heats the reaction zone. After reaching the process temperature, CH4 is introduced into the liquid metal via an alumina lance and methane decomposition occurs.
Nitrogen is injected in the gas space above the melt through a steel lance to cool this section and suppress unwanted reactions. The N2 flushing furthermore increases the gas volume flow and prevents the accumulation of solid particles in the piping section.
Pyrolysis carbon floats on the melt or is discharged in the produced gas stream. The off-gases leave the setup through a hot gas filter that separates residual solid particles collected in a glass container. The cleaned exhaust gases are analyzed using an infrared photometer and a thermal conductivity analyzer. A thermocouple located on the outside crucible wall allows continuous temperature monitoring during the experiments.
Different binary, ternary, and multicomponent alloys were analyzed regarding their efficiency in methane pyrolysis. The results are implemented in a statistical design of experiments developed using the software MODDE® 12.1. Thus, it is possible to describe the experimental results by multiple linear regression. Coefficients can be defined, which specify an applicable equation within the range of investigated compositions that can predict the achievable CH4 conversion rate for a given alloy and experimental time.
Calculations
Literature research has shown that effects enhancing the reaction yield in bubble column reactors can be correlated with lower surface tensions and viscosities as well as higher densities of the utilized liquids [3, 4]. Therefore, the densities in the alloying systems are approximated, and the surface tensions and viscosities are calculated using the Butler equation (cf. eq (1)) and the KRP equation (cf. eq (2)), respectively.

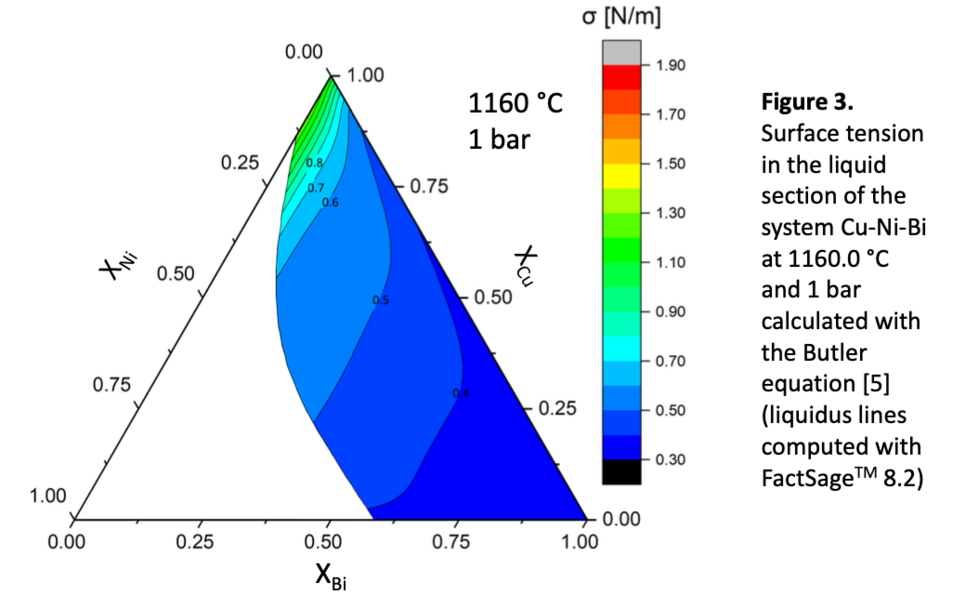
Figure 3 shows the results of the surface tension calculations in the liquid sector of the ternary system Cu-Ni-Bi. Here the lowest values can be found in the bismuth corner. The addition of nickel or copper leads to an increase in the computed values.
Results and discussions
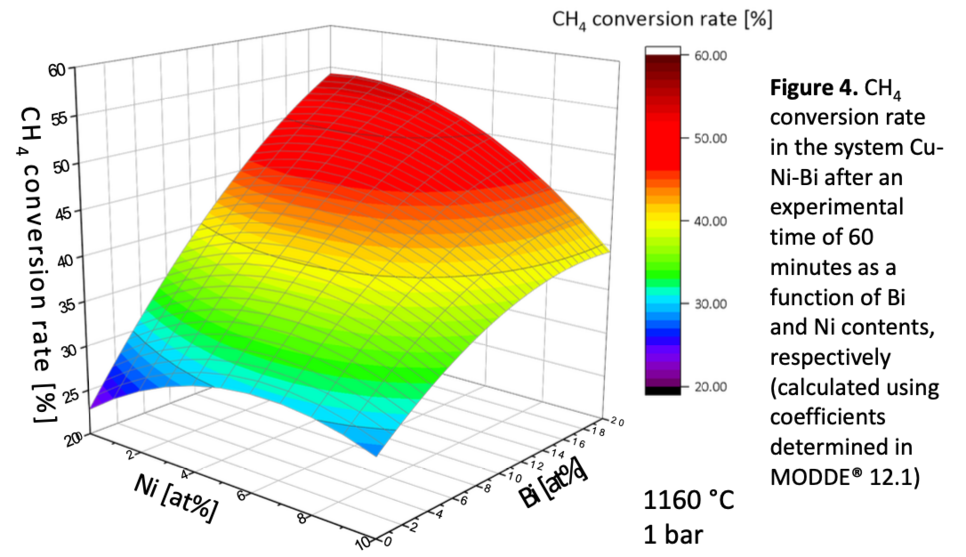
The achievable methane conversion for a specific alloy can be depicted as a function of the constituent metals’ content by implementing the experimental results in a statistical DOE. Figure 4 shows an exemplary graph for the system Cu-Ni-Bi at 1160 °C and 1 bar. The diagram depicts the lowest conversion rates for pure copper. As the Bi content increases, the methane conversion improves. Adding nickel to Cu-Bi initially boosts the reaction yield until a maximum is reached. Further increasing the Ni content leads to a decrease in the conversion rate. A comparison of the experimental and the computational results in combination with the statistical evaluation suggests that the effectivity of a specific alloy is the result of a superposition of the catalytic activity with several parameters affecting the reaction kinetics. Against this background, an increase in bismuth content results in an enhanced reaction kinetic due to the lower surface tension of the alloy, which could be the driving force of its conversion-improving effect. An excellent catalytic activity of nickel compensating adverse kinetic effects is a possible explanation for the positive effect of a small addition of nickel. At a higher Ni content, the disadvantages predominate.
Publications / Poster
References
[1] IEA, Global Hydrogen Review 2022, IEA, Paris (2022).
[2] M. Msheik, S. Rodat and S. Abanades, Methane Cracking for Hydrogen Production: A Review of Catalytic and Molten Media Pyrolysis. Energies 14 (2021), 11, pp. 3107. doi:10.3390/en14113107
[3] K. Mori, M. Sano and T. SATO, Size of Bubbles Formed at Single Nozzle Immersed in Molten Iron. ISIJ Int. 19 (1979), 9, pp. 553–558. doi:10.2355/isijinternational1966.19.553
[4] A.A. Mouza, G.K. Dalakoglou and S.V. Paras, Effect of liquid properties on the performance of bubble column reactors with fine pore spargers. Chemical Engineering Science 60 (2005), 5, pp. 1465–1475. doi:10.1016/j.ces.2004.10.013
[5] J.A.V. Butler, The thermodynamics of the surfaces of solutions. Proc. R. Soc. Lond. A 135 (1932), 827, pp. 348–375. doi:10.1098/rspa.1932.0040
[6] L.Y . Kozlov, L.M. Romanov, A.P . Pod'yachev, N.N. Petrov and O.V. Kostygova, Calculation of viscosity of multicomponent melts on iron and nickel base. Izv. Vyssh. Uchebn. Zaved., Chern. Metall;(USSR) 5 (1982)